Its great to have products selling very well that you have to replenish your inventory on regular basis but low stock levels displayed to customers can turn them away.
The ‘Receiving’ feature of CartSpark turns ‘low inventory’ and ‘out of stock’ quantities into an advantage by not only showing your customers when more products will become available but also letting them pre-order certain quantities from the scheduled product replenishment. You can calculate the actual Landing Cost of products, if you choose to add expenses such as shipping, import taxes, etc. to the original product cost. These expenses can be distributed as follows:
- By each product’s physical weight or cubic weight (ideal for shipping related expenses) (
- By percentage, which will distribute the fees evenly proportional to product price (ideal for import taxes, etc.)
- By flat rate, which will equally distribute expenses according to quantity of products.
This feature will also send emails to those customers who chose to be notified when an out of stock product becomes available.
To create a new Receiving manually click on ‘Create New‘ button on Receivings page of the Dashboard and start typing quantities and costs of each product or upload an Excel file to automatically import the data from that invoice (saved in .CSV format) by clicking “Create using CSV file” button.
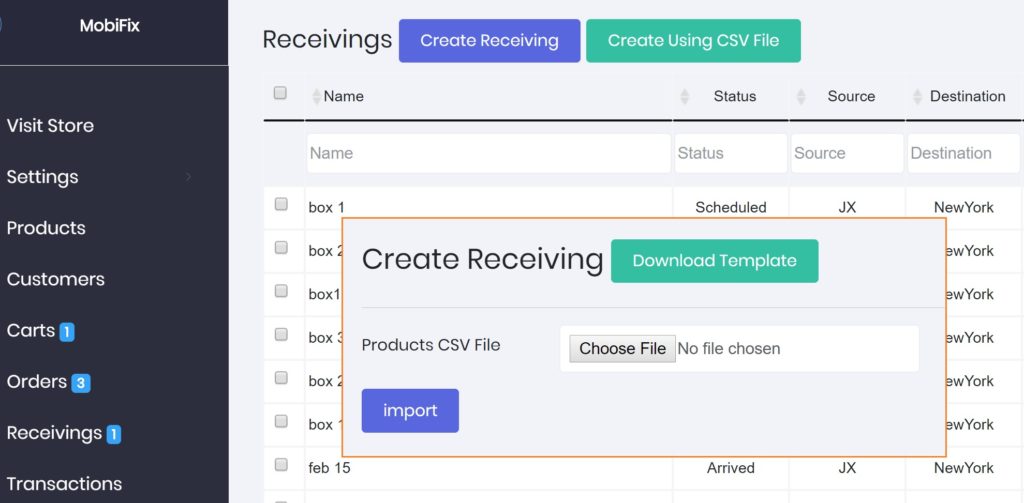
Copy the area with important contents of your attached invoice directly from your e-mail into an Excel spreadsheet and save it on your device as CSV (comma separated) file.
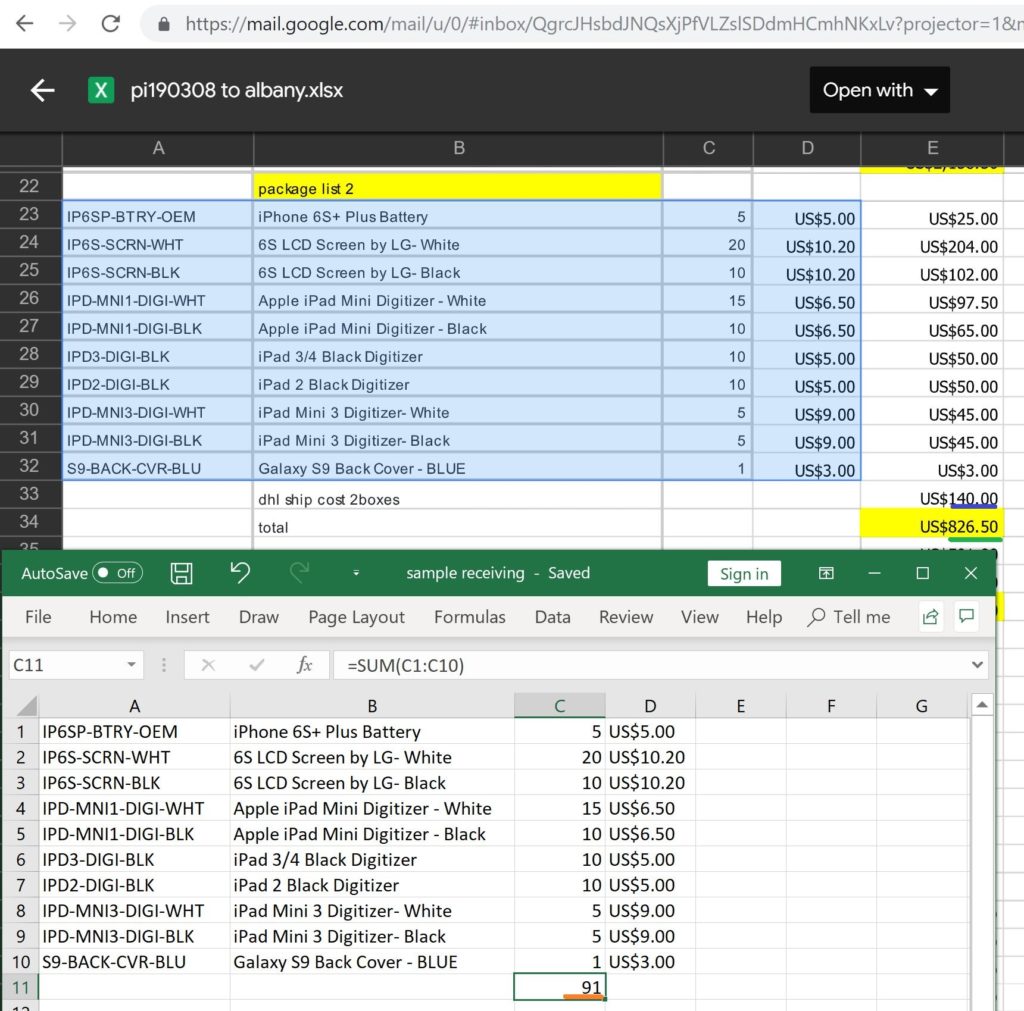
After the CSV file is imported all the invoice contents will be displayed in the fields which you can modify by editing existing or adding new line items as well as adding relevant expenses such as $140 shipping fee in this case.

Make sure the total amounts (underlined in green on both images: 826.50-140=686.50 dollars) and total product quantities (underlined in orange: 91 items) match the information on the original invoice. Select the option for shipping expenses (in this case shipping fees are selected to be added to product costs by their cubic weight) click ‘Next’ to see results.
On the next screen product are displayed with their old costs and quantities as well as the new costs that include fees. Select how you want the costs to be updated and choose a date when you expect this shipment to arrive and become available for customers to purchase using the ‘Schedule’ button.

Once you click the ‘Schedule’ button, the status of this Receiving will change to ‘Scheduled’ and your customers will be able to pre-order these products if your store runs out of stock on any of them. Scheduled receivings automatically change to ‘Arrived’ on the date selected and products will be added to stock (instead of just pre-order).

This enables customers to pre-order some of the incoming quantities if they attempt to add to cart more product than what was available in stock.
2,604 thoughts on “Receiving Products and Inventory Replenishment”
Comments are closed.